From Ruins to Residences
A Sustainable Approach to Construction Using Recycled Crushed Concrete
Engeo
The Opportunity
A project at Richmond Street, Petone, New Zealand, stands as a shining example of how repurposing recycled crushed concrete can deliver both economic and environmental benefits. By reusing materials from a demolished cigarette factory on-site, this project not only saved on resources and transportation costs but also contributed to a greener future.
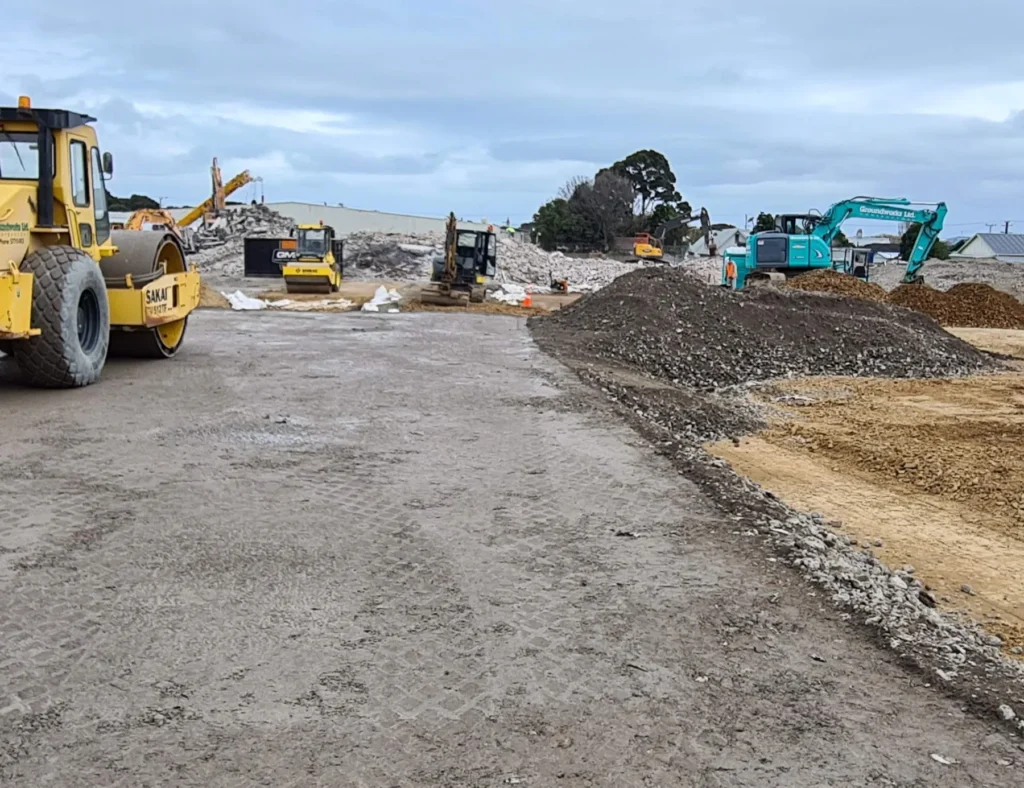
Repurposing the Cigarette Factory
At Richmond Street crushed concrete from the demolished cigarette factory was repurposed as engineered fill for new townhouse residences.
The following steps were taken:
- Demolition and Sorting: The cigarette factory building was carefully demolished, and the concrete debris was sorted to separate the crushed concrete from other waste materials.
- Crushing On-Site: To maximize efficiency and minimize transportation, the concrete from the demolished building was crushed on-site. This allowed for immediate repurposing of the material without the need for additional transportation or processing.
- Metal Rebar Removal: The metal rebar, a common component in reinforced concrete structures, was meticulously extracted from the crushed concrete to ensure the quality and usability of the recycled material. The metal was sent offsite for recycling.
- Engineering and Compaction: The crushed concrete was then placed and compacted as engineered fill beneath the floor slabs of the new townhouse residences. This provided a solid and stable foundation for the construction.
A Different Approach
When faced with the demolition of the former cigarette factory building at Richmond Street, engineers recognized a unique opportunity. Instead of treating the demolished structure as waste, they saw its potential for reuse in the earthworks for construction of new townhouse residences. By repurposing the crushed concrete and removing the metal rebar, they could eliminate the need to purchase new fill materials and avoid the associated transportation costs. This forward-thinking approach presented a win-win situation, reducing project expenses and minimizing environmental impact simultaneously.
Key Learnings
The Richmond Street project offers valuable insights for the construction industry, highlighting the following key learnings:
- Reuse Opportunities: Demolished structures present a valuable resource for future construction projects. Identifying opportunities to repurpose materials can save costs and reduce environmental impact.
- Collaboration and Planning: Effective collaboration between demolition and construction teams is crucial to identify and extract reusable materials. Early planning ensures seamless integration of recycled materials into the new construction.
- Quality Control: Rigorous sorting and extraction processes, such as removing metal rebar, are essential to ensure the quality and suitability of recycled materials for use in construction.
- Sustainability and Cost Efficiency: Embracing sustainable practices not only benefits the environment but also contributes to cost savings. By reducing the need for new materials and transportation, projects can become more economically viable.
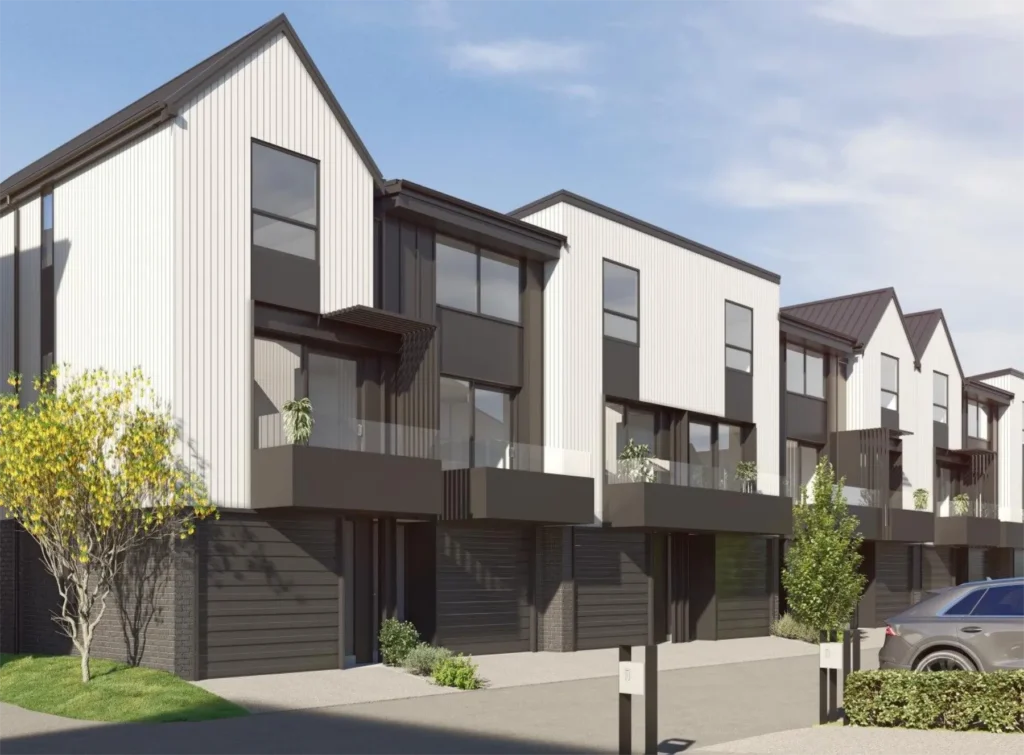