One-Part Mix Geopolymer Concrete with Waste Glass Aggregates
Ailar Hajimohammadi, Taehwan Kim, and Stephen Foster
The opportunity
The production of Portland cement, a key component in concrete, generates significant carbon emissions, with one ton of ordinary Portland cement (OPC) producing approximately 0.85 tons of CO2. An alternative to cement as a binder in concrete, is geopolymer technology, which uses industrial by-products to create binders that can substitute for cement in concrete. The processes of binding in geopolymer gels and cement hydration are significantly different. In geopolymer formation, the initial step involves activating aluminosilicate precursors using alkaline solutions. Subsequently, the dissolved alumina and silica components undergo stages of speciation, gelation, reorganisation, and polymerization, eventually leading to the development of a cross-linked three-dimensional structure.
In addition, incorporating waste glass in geopolymer concrete (GPC) addresses sand scarcity and aids waste reduction. While finely crushed glass can substitute for natural sand, managing alkali-aggregate reaction is crucial. Glass particles, known for durability and resistance, prove valuable alternatives to natural aggregates, influencing concrete strength development through filler activity and matrix densification. This approach combines environmental benefits with innovative materials in the construction industry.
Research objectives
UNSW researchers, in partnership with industry collaborators, innovatively formulated and tested an eco-friendly geopolymer concrete (GPC) for footpath slabs and kerbs. The project aimed to create a user-friendly, one-part mix design, mirroring the simplicity of traditional cement use. This involves preparing the concrete mix by adding water, making it accessible and straightforward. The geopolymer mix utilized industrial by- products such as fly ash and slag as aluminosilicate precursors, contributing to sustainability. Notably, the GPC also integrated glass aggregate, showcasing a commitment to incorporating environmentally conscious materials in construction practices.
Initial findings
- Glass content. Findings for different glass percentages (25%, 50%, and 75% of fine aggregate) indicate a decrease in strength with increased glass content as shown in the graph below.
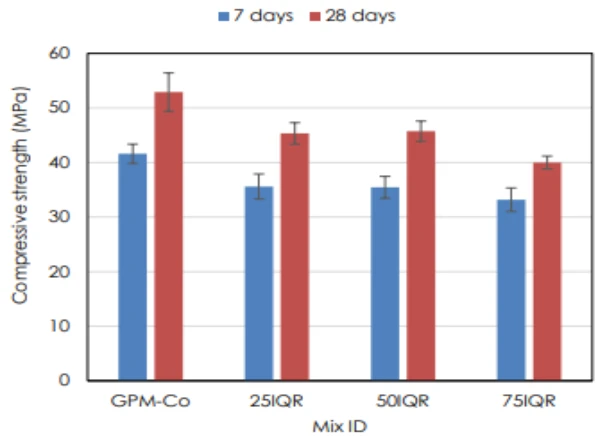
- Slump retention. GPC exhibited no flash set within the initial 90 minutes, and the slump remained above the specified minimum of 90 mm.
- Durability: The geopolymer binder in this project doesn’t cause excessive expansions from Alkali-Aggregate Reaction (AAR). However, compared to control concrete, GPC specimens with 13% glass exhibit increased carbonation depth.
- Laboratory Strength. Despite having 13% glass aggregate, the mix achieved approximately 10% higher compressive strength at 28 days compared to the control concrete.
- Field Compressive Strength: Field trial samples (GP-13G) displayed lower strength at 7 and 28 days compared to lab mixes (see graph below), likely due to on-site water addition for workability. Further investigation is ongoing.
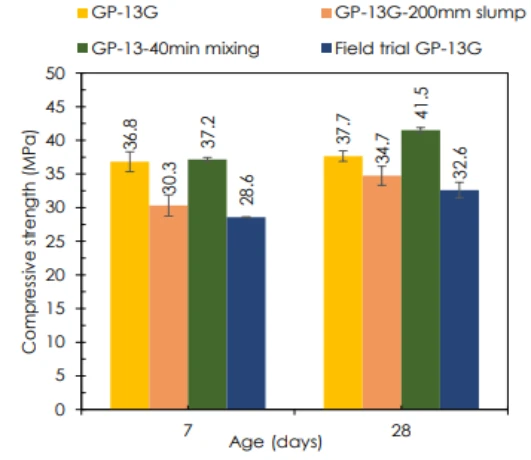
Key learnings
- The GPC, which incorporated glass aggregate developed in the UNSW Infrastructure Laboratory, was successfully implemented on-site at a larger scale.
- Comparing the laboratory trials and field experiences, the mix design and batching process can be adjusted for the best performance. However, employing a higher water quantity than the recommended dosage led to an immediate significant increase in a slump and a subsequent decrease in strength.
- Nevertheless, the mixture used in the field was successfully placed, compacted, and finished, demonstrating no indications of shrinkage cracks within the initial four weeks following placement. Laboratory test results show drying shrinkage and AAR expansion are well below their allowable limits.
- The field trial, featuring 13% glass aggregate (GP-13G), holds promise as a valuable material for footpath and pavement construction.
- Collaboration between research teams and the industry holds the potential for mutually beneficial contributions to the advancement and delivery of such products.